Some business owners think that their manufacturing shop will look more productive if employees are moving about briskly, raw materials are stacked in every available space, and scrap is piling up near production equipment. Nothing can be further from the truth, because smart buyers see chaotic businesses as a potential risk.
If you are thinking about selling your business at some future date, you should take steps now to implement industry proven steps to a more efficient workplace. The best approach is to embrace the core principles of Lean Manufacturing (“Lean”). This will give you a great story to tell buyers who already understand the value of this well-known approach. There are many additional business benefits to embracing Lean:
- A safer workplace
- Fewer production defects
- Reduced costs
- Increased production flexibility
- Better employee morale
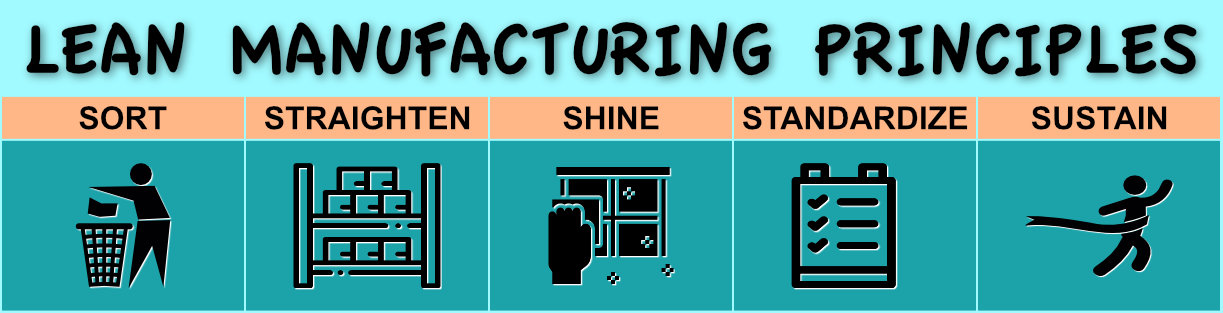
What is Lean Manufacturing?
Lean Manufacturing embodies common-sense tactics that have been around far longer than the formal methodology. It embraces the innovations of Henry Ford’s production line and the Toyota Production System.
Some businesses hire a team of consultants to embrace the lean manufacturing methodology, but you can implement Lean without making it a big and costly initiative. In fact, you may find that you have already adopted some of Lean’s core tenets, because the goal of lean manufacturing is to relentlessly and continuously eliminate waste from your business: wasted time, wasted motion, wasted effort wasted materials, wasted management intervention, and wasted over processing. The starting point for achieving this goal is implementing Lean’s 5S’s, which are Sort, Straighten, Shine, Standardize and Sustain.
1. Sort
Look around your shop floor and front office. Remove everything that is unnecessary and move things that are rarely used to an out-of-the-way long term storage area. Discard outdated catalogs, unused or broken tools, equipment that no longer works, old furniture, outdated files (both paper and electronic), and anything you retained “just in case” for more than a few years.
Categorize and group the remaining items.
2. Straighten
“A place for everything and everything in its place.”
Everything that remains after the initial sort should have a designated location: no more unlabeled boxes under desks, in hallways, and on stairwells. When employees are done using a tool or referring to a file, these items must be returned to their designated storage location. Everyone who needs to use these items will know exactly where to find them, and will waste no time in retrieving them.
Use shelving and labeling that is appropriate for the item and label the storage locations. Provide employees with a safe place to store their belongings during their work shift. Lean Manufacturing will Place heavy items closer to the floor so there is no need to go get a ladder to retrieve them. To keep production moving at a lively pace, make sure employees can find the tools they need within a reasonable length of time.
3. Shine
A clean workplace is inherently more productive, and it’s a shared responsibility. If dirt and dust tend to accumulate in your shop, identify the causes and take action. Make it easy for employees to keep their work areas clean by providing cleaning tools and supplies nearby. Every work shift should end with 5-15 minutes of cleanup time so that the next shift can begin to work efficiently.
Establish designated work areas for each production step so that clutter doesn’t intrude and distract. Other items, such as windows, walls, lighting, ductwork, display cases, and computer workstations should be cleaned on an established schedule.
4. Standardize
In addition to keeping your workplace clean of dust, dirt, and debris, there is additional benefit from keeping it neat. Workers will know where everything belongs and won’t waste time searching for the right tools or paperwork. Incorporate visual cues with posters, labels and color-coding. Adopting standard locations, configurations and standard operating procedures will reduce the need for ad hoc meetings and crisis management. Checklists for periodic maintenance procedures will help make sure equipment is peak in top working order.
You will be able to see abnormalities in your shop when you see anything “out of place.” This will allow you to pinpoint employee and equipment issues that require your intervention. When standards can be put in place across production areas, it will be easier to move employees from station to station. Standards also make your workplace safer.
5. Sustain
The last tactic is often most difficult – sustaining the lean manufacturing standards. When business is booming and people are rushing to meet delivery dates or address quality issues, there is a tendency to cut corners and revert to practices that are more chaotic. It requires management commitment and encouragement to maintain the efficiency gains that lean manufacturing can provide.
Educate along the way to encourage employees to understand that the lean principles of sort, straighten, shine and standardize will make their work easier in the long run. Remember that the adoption of all these principles will take some time to become habits. Make sure managers know that they are responsible for implementing and auditing against these standards in their work areas. Recognize and reward those employees who work within the lean framework and suggest additional improvements. Let employees know that lean manufacturing is a system of continuous improvement and actively seek out their input.
Take it a Step Further
There is more to lean manufacturing than the 5S principles, but they are the best way to start incorporating Lean on your own, without pursuing certifications or hiring consultants. A lean manufacturing process includes only those steps that add value from the customer’s perspective and creates flow by establishing pull from one workstation to the next. After this flow is established, the business works relentlessly to reduce the amount of time to complete each step. Here are two helpful links to help you deepen your understanding of Lean.
Lean Manufacturing’s Impact on the Sale of Your Business
In a previous blog post, we urged you to adopt the common-sense principles of lean manufacturing without referring to them as Lean’s 5S’s. Buyers will be reassured by your clean, efficient, and orderly workplace. You will have a great story to tell about how Lean is helping you continuously improve your profitability.
If you have additional questions about how lean manufacturing can help you prepare for the sale of your business, contact us at info@acceleratedmfgbrokers.com.